by Sylvain Lefebvre
Consumer level 3D printing holds great promise for the future [1]. However, few people possess the required skills and time to create elegant designs that conform to precise technical specifications. “By–example” shape synthesis methods are promising to address this problem: New shapes are automatically synthesized from existing ones, by deforming or assembling parts cutout of examples.
The ShapeForge project, funded by the European Research Council (“Starting Grant Project”), aims at helping users design new, complex objects from examples. The goal is to preserve the appearance of the examples while ensuring that the newly generated objects enforce a specific purpose, such as supporting weight distributed in space, standing balanced in a specific position, or providing storage spaces. Such constraints are crucial for designing many of the common objects surrounding us: containers, enclosures, various parts with mechanical functions; but also for artists and enthusiasts wishing to fabricate interesting, surprising objects. We also consider fabrication constraints: There are several limitations to the additive manufacturing processes, such as minimal thickness or maximal overhang angles. We therefore investigate algorithms that can turn a virtual object into a design that can be fabricated.
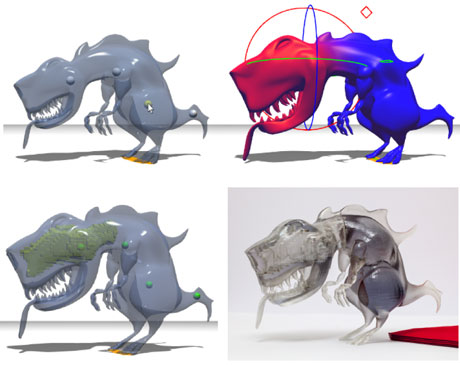
As an example of our methodology, we recently developed, in collaboration with ETH Zurich, a method for balancing 3D models [2]. Many artistic 3D objects designed on a computer are created without any special consideration for the laws of physics. As long as the models remain in a computer this is of no consequence. However, fabrication through 3D printing breaks the illusion: printed models topple instead of standing as initially intended. We aimed to assist users in producing novel, properly balanced designs. Balance optimization is formulated as an energy minimization, improving stability by modifying the volume of the object, while preserving its surface details. Our optimizer combines two operations changing the mass distribution of the object: Carving and deformation. This takes place during interactive editing: the user cooperates with our optimizer to achieve the end result. With our technique, users can produce fabricated objects that stand in one or more surprising poses without requiring glue or heavy pedestals, as illustrated Figure 1.
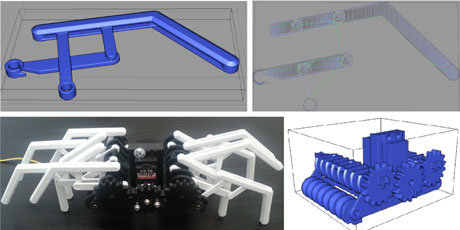
The ShapeForge project requires a full understanding of the creation pipeline, from the modelling of the object to the fabrication on the 3D printer. We are developing an innovative CAD software for additive manufacturing [3]. It starts from a description of an object in terms of Boolean operations between solids (union, difference, intersection) and directly generates the instructions driving the printer. Our software is especially well-suited for combining parts from existing designs, as well as dealing with shapes with complex, intricate geometries. Most importantly, our software erases the boundaries between modelling and the printing process, letting us develop novel approaches considering both issues simultaneously. Figure 2 illustrates a spider robot designed with our publicly available.
With ShapeForge we hope to bring novel ways to model complex shapes, developing algorithms that handle the difficult task of finding a compromise between the intention of the designer, the technical requirements of the fabrication process, and the function of the final, real object.
Links:
IceSL: http://webloria.loria.fr/~slefebvr/icesl/
Walking robot: http://www.thingiverse.com/thing:103765
References:
[1] H. Lipson, M. Kurman: “Factory@home: The emerging economy of personal fabrication”, Report Commissioned by the Whitehouse Office of Science & Technology Policy, 2010, http://kwz.me/7H
[2] R. Prévost et al.: “Make it Stand”, in proc. of SIGGRAPH (2013), http://dx.doi.org/10.1145/2461912.2461957
[3] S. Lefebvre: “IceSL: A GPU Accelerated modeler and slicer”, in proc. of AEFA 2013,
http://webloria.loria.fr/~slefebvr/icesl/icesl-whitepaper.pdf
Please contact:
Sylvain Lefebvre,
Inria Nancy - Grand Est, France
E-mail: