by Alexander Hanzlik and Erwin Kristen
The increasing complexity of electronic control systems requires new methods for design, analysis and test of such systems. The DTFSim Data Time Flow Simulator developed at the Austrian Institute of Technology is a discrete-event simulation environment for model-based design, analysis and test of networked control systems for automotive applications.
Automotive Networked Control Systems
An automotive control system consists of a set of devices that control one or more functions of the vehicle, such as an electronic brake. Modern automotive control systems are networked control systems (NCS). A typical NCS contains the following components:
- Sensors to acquire information from the physical environment
- Controllers to provide decision and commands
- Actuators to perform the control commands
- Communication network for information interchange between sensors, controllers and actuators
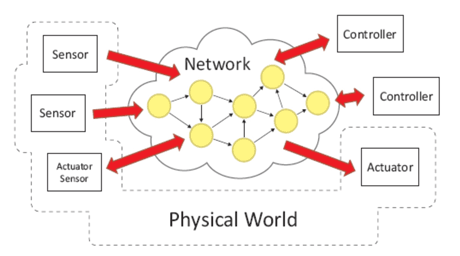
In an NCS, control and feedback signals are exchanged among the different system components in the form of information packages through the communication network.
Principle of Operation
The DTFSim is based on the idea that a NCS can be built by repetitive use of the following parts:
- Component part: Components are typically a piece of hardware, such as an ECU, a sensor or an actuator. Each component executes one or more functions. Components are spatially separated and connected via direct links (wire) or a communication network.
- Network part: The network part is responsible for communication between components that are not directly linked. This part comprises the network architecture and the network protocol, such as an Ethernet bus.
- Function part: The function part contains the implementation of the component functions, for instance, a brake torque calculation algorithm.
- Timing part: The timing part contains the timing properties of the system, such as the worst-case execution times of component functions.
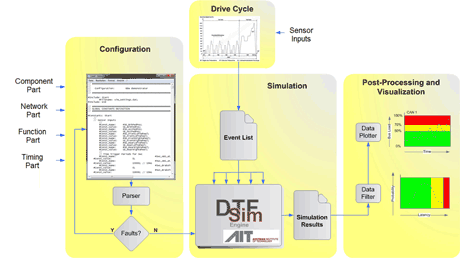
The system architecture, consisting of the component part and the network part, is built using elements from a modular assembly system provided by the DTFSim. These elements are grouped together to from more complex structures, such as an ECU or an Ethernet bus. Typical elements are sensors, processors and actuators. Component functions (function part) are added to the different elements to be able to perform specific control tasks. Finally, each element has a propagation delay (timing part).
DTFSim models consist of “event chains”, where an event chain is a directed path from a sensor to an actuator, with an arbitrary number of elements in between. The simulation aims to determine essential system characteristics, such as the bus load (the load of the communication network) and the control signal latencies (the propagation times of control signals from sensors to actuators). This is achieved by stimulating the system at the model inputs (sensors) and by observing the event and data flow along event chains over time to the actuators.
DTFSim Workflow
A typical workflow comprises the following steps:
- Configuration: The first step is the generation of the system configuration, which consists of the system architecture (component and network part) and the system behaviour (function and timing part).
- Drive Cycle: A drive cycle consists of a set of input events for each sensor of the system, e.g., the different positions of the vehicle brake pedal during simulation. The sum of all input events is an event list used for stimulation of the system.
- Simulation: Based on the configuration and the drive cycle, the simulation is executed until all events have been processed. Each event that occurred during simulation is stored in the simulation results log file.
- Post-Processing and Visualization: The last step is the post-processing of the simulation results. In this step, data of interest is extracted from the simulation results log file. This data is then used to produce visualizations of system characteristics of interest, such as the bus load over simulation time or the propagation time distributions of dedicated control signals.
Current Applications and Future Work
The DTFSim has been developed in the course of the EU ARTEMIS project POLLUX, which was related to the design of electronic control systems for the next generation of electric vehicles. Currently, the DTFSim is deployed in two EU ARTEMIS projects: In MBAT (Combined Model-based Analysis and Testing of Embedded Systems), the DTFSim is deployed in an automotive used case where the performance of an electronic braking system is analyzed by means of a simulation model. In CRYSTAL (Critical System Engineering Acceleration), the DTFSim is also deployed in an automotive use case where it is used for timing analysis of an automatic speed limitation application.
Future work relates to the integration of the DTFSim into an automated verification and validation process for embedded control systems.
Links:
http://www.mbat-artemis.eu/home/
http://www.crystal-artemis.eu/
Reference:
[1] A. Hanzlik, E. Kristen: “A Methodology for Design, Validation and Performance Analysis of Vehicle Electronic Control Systems”, in proc. of AMAA 2013, Berlin
Please contact:
Alexander Hanzlik, Erwin Kristen, AIT / AARIT, Austria
E-mail: