by Paolo Cignoni, Nico Pietroni, Luigi Malomo and Roberto Scopigno
Mesh joinery is an innovative method to produce illustrative shape approximations suitable for fabrication. Mesh joinery is capable of producing complex fabricable structures in an efficient and visually pleasing manner. We represent an input geometry as a set of planar pieces arranged to compose a rigid structure by exploiting an efficient slit mechanism. Since slices are planar, a standard 2D cutting system is sufficient to fabricate them.
Over the last decade, a variety of rapid prototyping technologies have been developed to support the manufacturing process, especially for the fabrication of production-quality parts in relatively small numbers. However, while the printing resolution has improved substantially - and consequently, the accuracy in terms of reproduction has reached high standards - rapid prototyping is still perceived as being too expensive for the mass market. This is particularly true for large scale reproduction: only a few techniques can produce, even approximated, large scale actual copy within reasonable cost and time bounds.
We have introduced mesh joinery [1], a novel and practical approach to fabricate illustrative shape approximations made up of several interlocked planar pieces, called ‘slices’. Slices can be easily fabricated even in large scale (both numbers and dimensions) using any 2D cutting device and then manually assembled through a sequence of simple well defined operations to obtain a rigid structure that resembles an input 3D model.
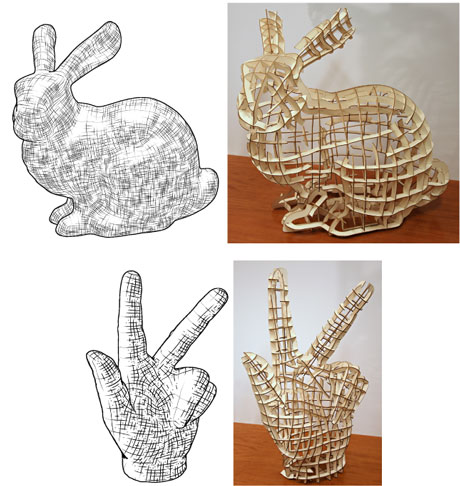
Figure 1: Starting from a 3D model with a cross field the Mesh Joinery approach allows to automatically generate flat cut arrangments that well approximate the original shape.
Our approach offers a truly low-cost solution owing to the simple cutting technologies employed and the relatively inexpensive material used (such as cardboard). Although the proposed slice structure approximates the original geometry and it cannot be considered as a ‘exact physical copy’, nevertheless, we believe that our method is attractive in many markets, such as in artistic or illustrative contexts, large scale approximate reproductions, free form scaffolding, and even in puzzles or toys, and where assembly is a key part of user experience.
Our approach is based on building interlocking arrangements composed of shallow flat ribbon-shaped pieces that follow a cross-field defined on the surface. We provide a novel formalism to automatically design a slice-to-slice interlocking system. This formalism provides enough degrees of freedom to follow complex cross-fields and, consequently, to efficiently approximate the global structure that characterizes the input shape. We also redesigned the traditional slit interlocking mechanism that is used to connect pieces in order to approximate generic 3D surfaces with greater flexibility. Additionally, we ensure a sufficient degree of physical stability of the final structure and provide the sequence of manual operations required for the assembly procedure.
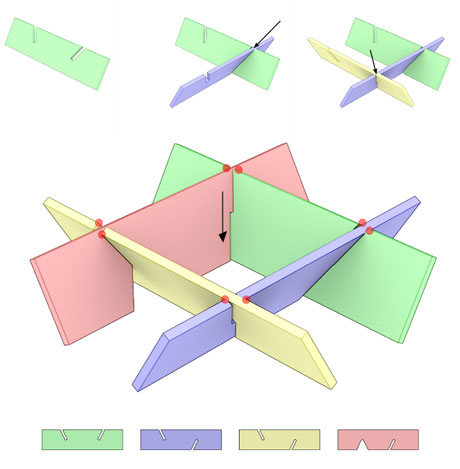
Figure 2: Mesh Joinery is based on a novel slit based interlocking system that allows to connect flat pieces in a much more flexible way and that retains robustness through global relationships.
Specifically, Mesh Joinery makes three major contributions that make it a significant advance in the field of large scale fabrication technologies.
First, we have extended the classical slit interlocking mechanism by providing additional structural degrees of freedom. In particular, we allow insertion movements that are not orthogonal to slices. In addition, we formulated non-orthogonal slice placement in a novel, structurally sound perspective. This new, more flexible, interlocking mechanism allows different slices to be connected without the traditional very limiting orthogonality constraints. These additional joinery degrees of freedom can be effectively exploited to represent complex models with few ribbon shaped slices that can run in the best way to approximate the original shape, far better arrangements to be generated than the current state of the art [2].
Second, we have introduced an efficient automatic strategy to approximate a surface with a set of slices. Slice placement is driven by an input cross-field [3] that represents in a compact, intuitive way the curvature flow over the surface. Our approach provides a set of appealing, uniformly distributed polylines lying on the surface of a mesh and agreeing with the given cross field. This curvature driven placement is very important to catch, with just a few pieces, the overall shape of the input object. In addition, the method takes into account slice insertion constraints and, while it does not theoretically guarantee that the mounting sequence is collision free, it yields arrangements that are practically assemblable and that exhibit a sufficiently robust slice structure. Our method may also take advantage of field symmetrization techniques for a better perception of the global structure of the object.
Finally, mesh joinery exploits an automatic procedure to ensure that the slice structure is physically achievable. First, it improves the final rigidity, acting upon the slit interlocking mechanism. Second, it ensures that the slice structure conforms to the physical constraints required by the manual assembling procedure. This procedure is specifically designed to deal with our extended slit mechanism.
The Mesh Joinery approach has been patented and it has been used in practice to build a number of real large models that have been shown at international conferences and workshops.
Link:
http://vcg.isti.cnr.it/Publications/2014/CPMS14/
References:
[1] P. Cignoni, N. Pietroni, L. Malomo, R. Scopigno: “Field-aligned mesh joinery”,. ACM Trans. Graph, 33, 1, (February 2014).
[2] Y. Schwartzburg , M. Pauly: “Design and optimization of orthogonally intersecting planar surfaces”, Computational Design Modelling, 2012.
[3] D. Panozzo, Y. Lipman, E. Puppo, D. Zorin: “Fields on symmetric surfaces”, ACM Trans. Graph. 31, 4 (July), 2012.
Please contact:
Paolo Cignoni
ISTI-CNR, Italy
E-mail: